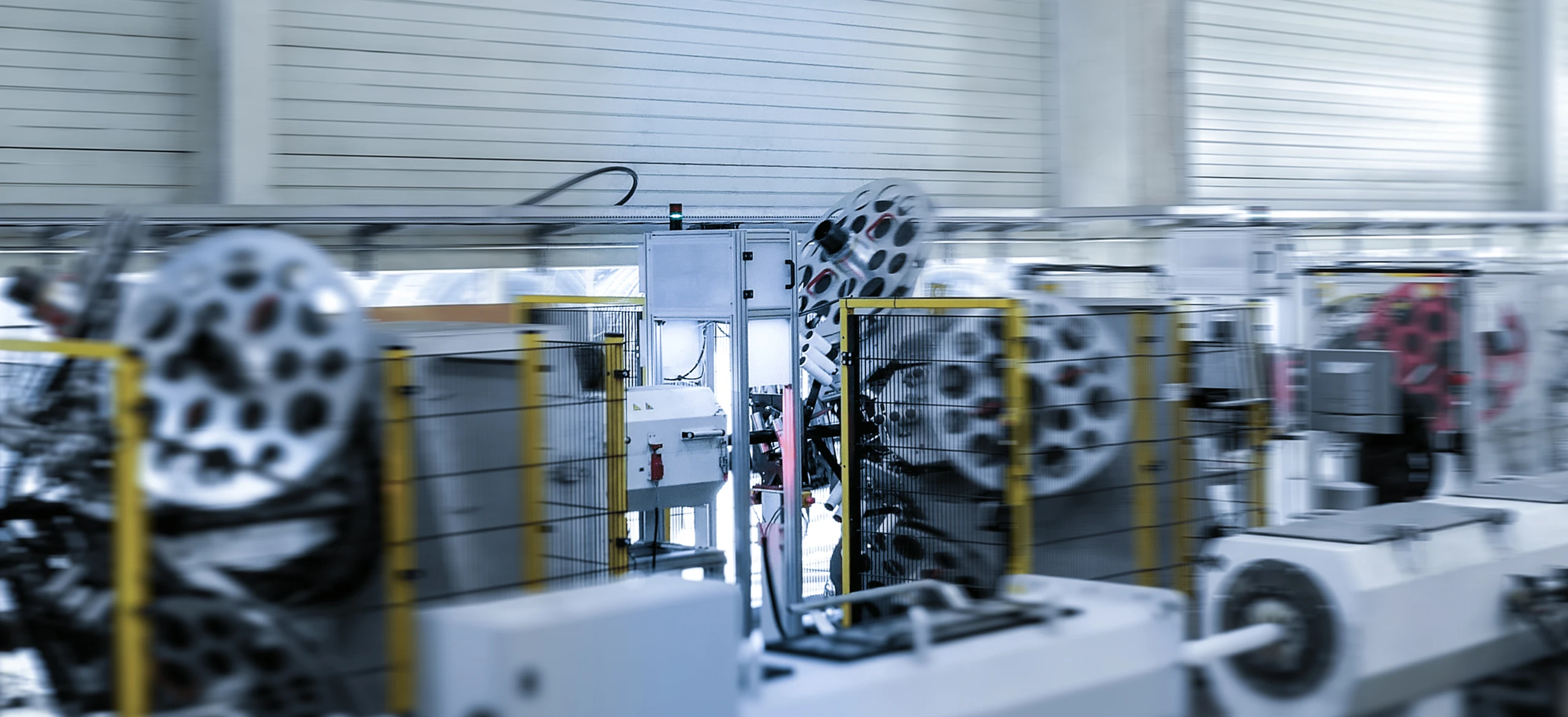
AI-Powered automatic tape placement
A Revolution in Pipe Quality Control and Inspection
Challenge
FibronPipe GesmbH, a leading thermoplastic composite pipes (TCPs) manufacturer, needed to ensure the precise placement of every winding of fiber tape around the pipe during production. The correct placement of the tape is critical to the properties of the final produced pipe, as placing the tape wounds far from each other creates “gaps”, while placing the tape wounds too close creates “overlays”. Both gaps and overlays compromise the structural integrity of TCPs under operational stress and pressure, hindering their longevity in the field. FibronPipe produces pipes of diverse widths (DN50 up to DN125) at high temperatures, with single and double winding stations producing minimal color differentiation between lower and upper layers of tape placement (e.g. black on black tape).
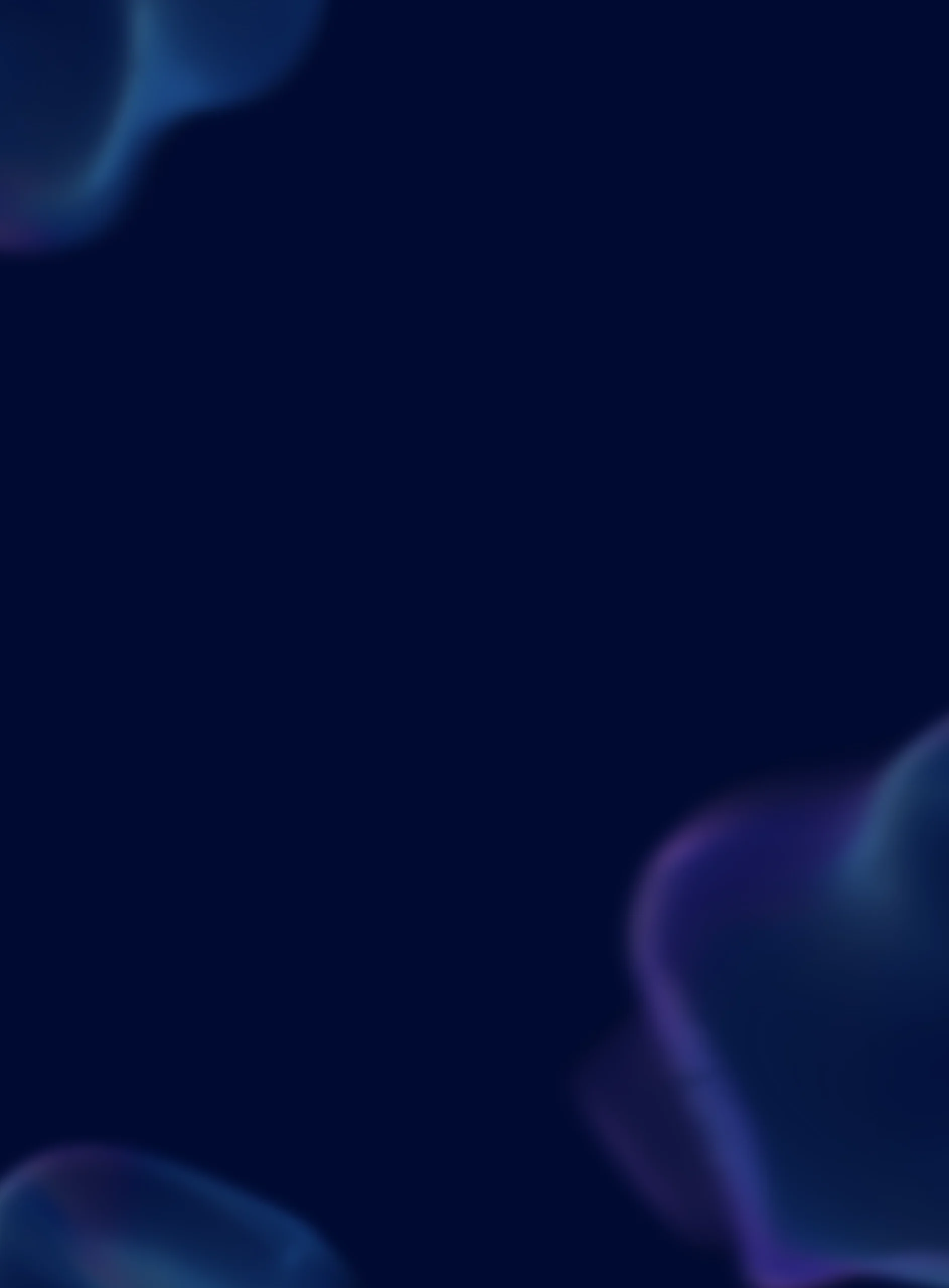
Solution
Ceyeborg’s solution was to develop a custom “open” inspection station design to allow seamless integration into the production line of FibronPipe. The open design allowed different pipe widths to be easily integrated into the same inspection station without modifications and minimized the risk of physical damage to the pipe in case of mechanical movement or “swinging” during production. The inspection station was designed to be shallow in depth, allowing FibronPipe to integrate it with a minimal extension to their production line’s length.
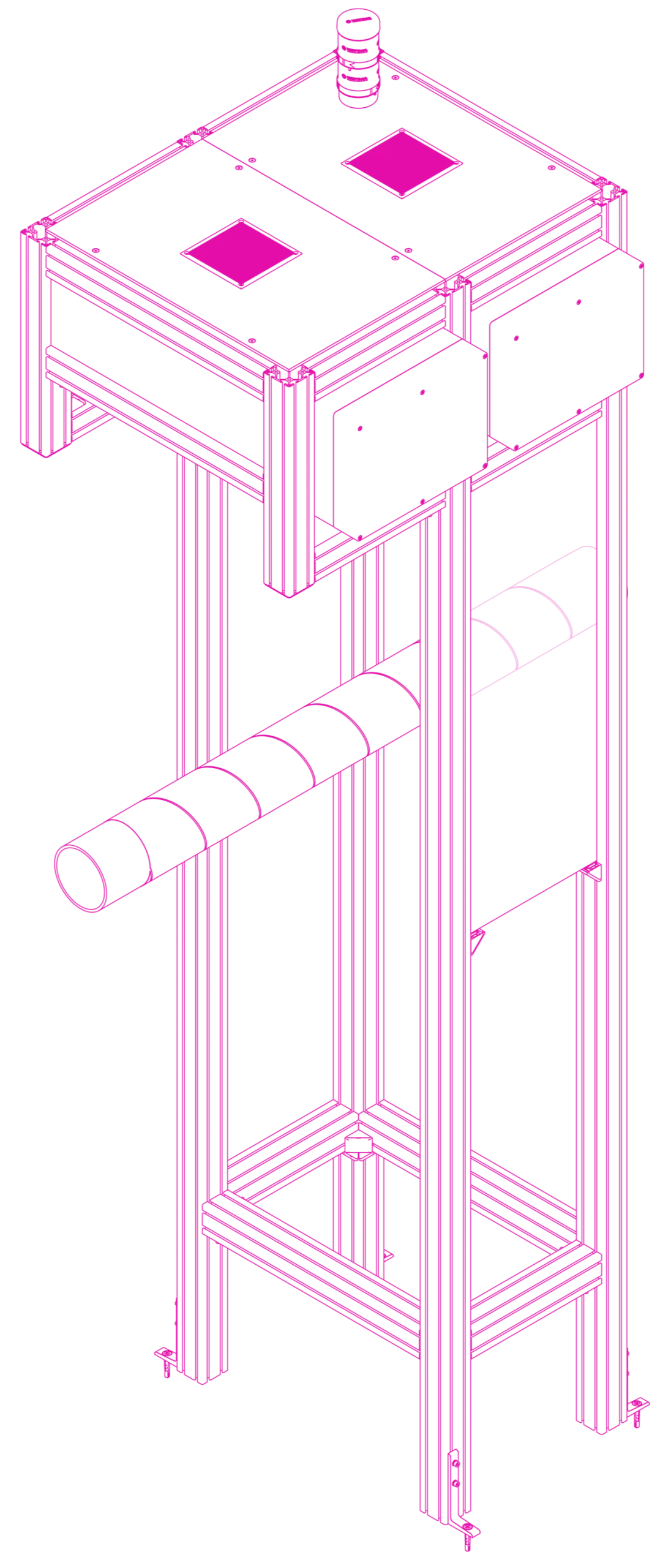
Custom “open-design” inspection station
To accommodate the production conditions of high-temperatures and a wide-range of produced pipe widths, Ceyeborg engineered a custom 2-axis movement mono-camera solution that is insensitive to infra-red heat compared to laser-based solutions. The 2-axis camera allowed for free movement of the sensor setup after the installation of the inspection station, such that changes in the exact position and width of the pipe were no issue to capture within the moveable camera’s field-of-view. The 2-axis camera setup was controlled by Ceyeborg’s AI-based computer vision software through a custom designed PCB and ECU.
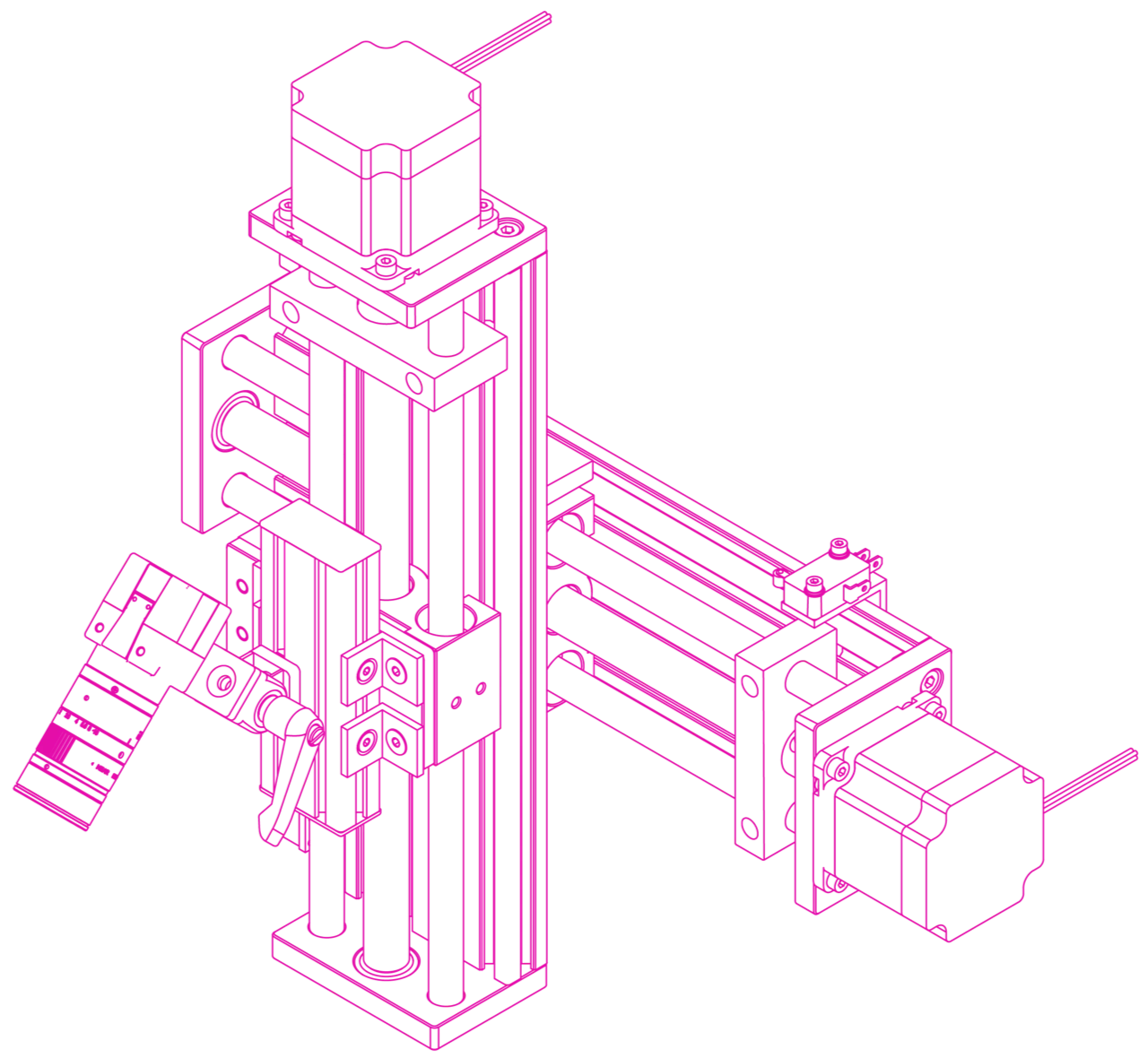
CBORG MARK I – 2-Axis Camera
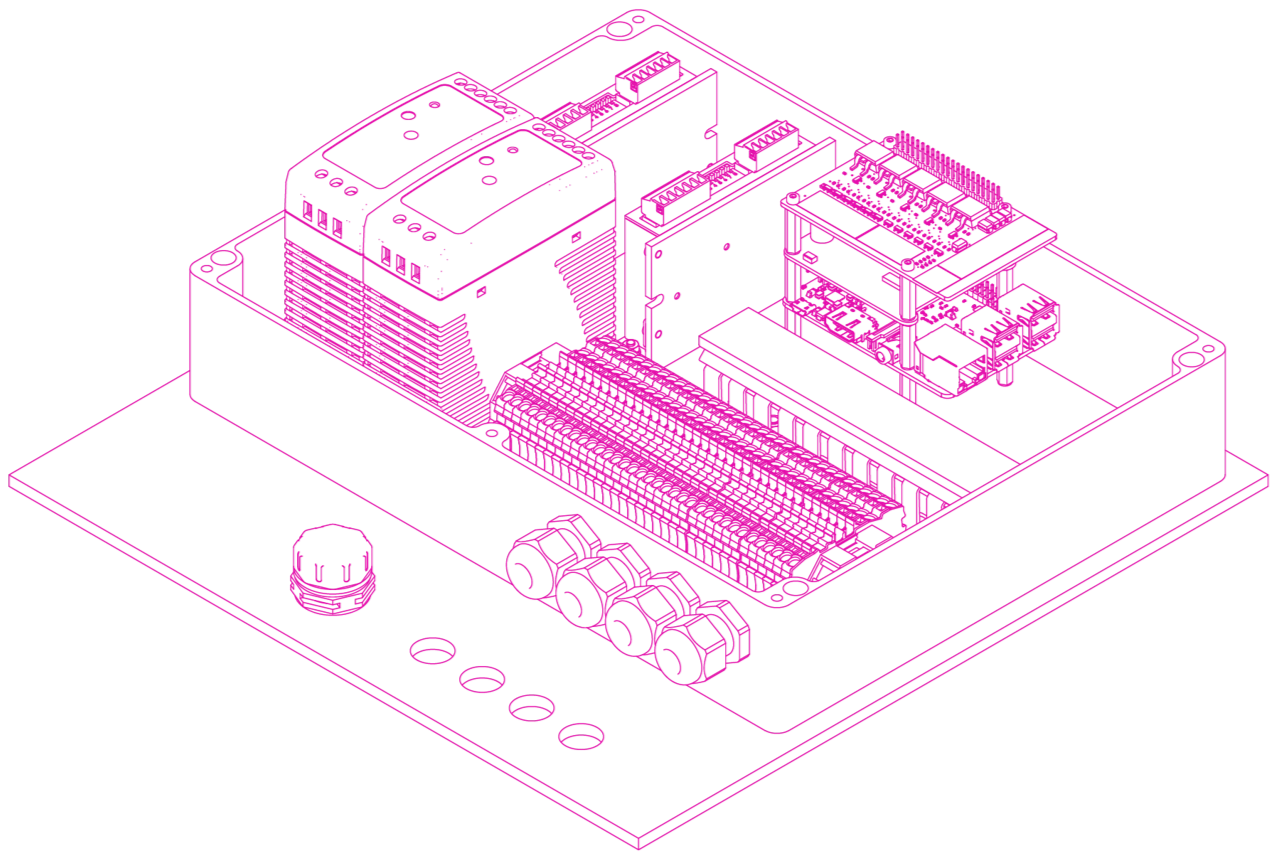
Custom PCB and ECU in Distribution Box
The challenge of detecting gaps and overlays of same color is difficult to solve with pure classical computer vision methods. Ceyeborg developed a custom semantic segmentation AI-model coupled with classical computer vision-based post processing to achieve an optimal mix of cutting-edge and mature techniques to solve the problem at hand. The overall software solution was able to deliver the semantic predictions of the observed tape placement features, as well the exact millimeter dimensions of the feature instances.
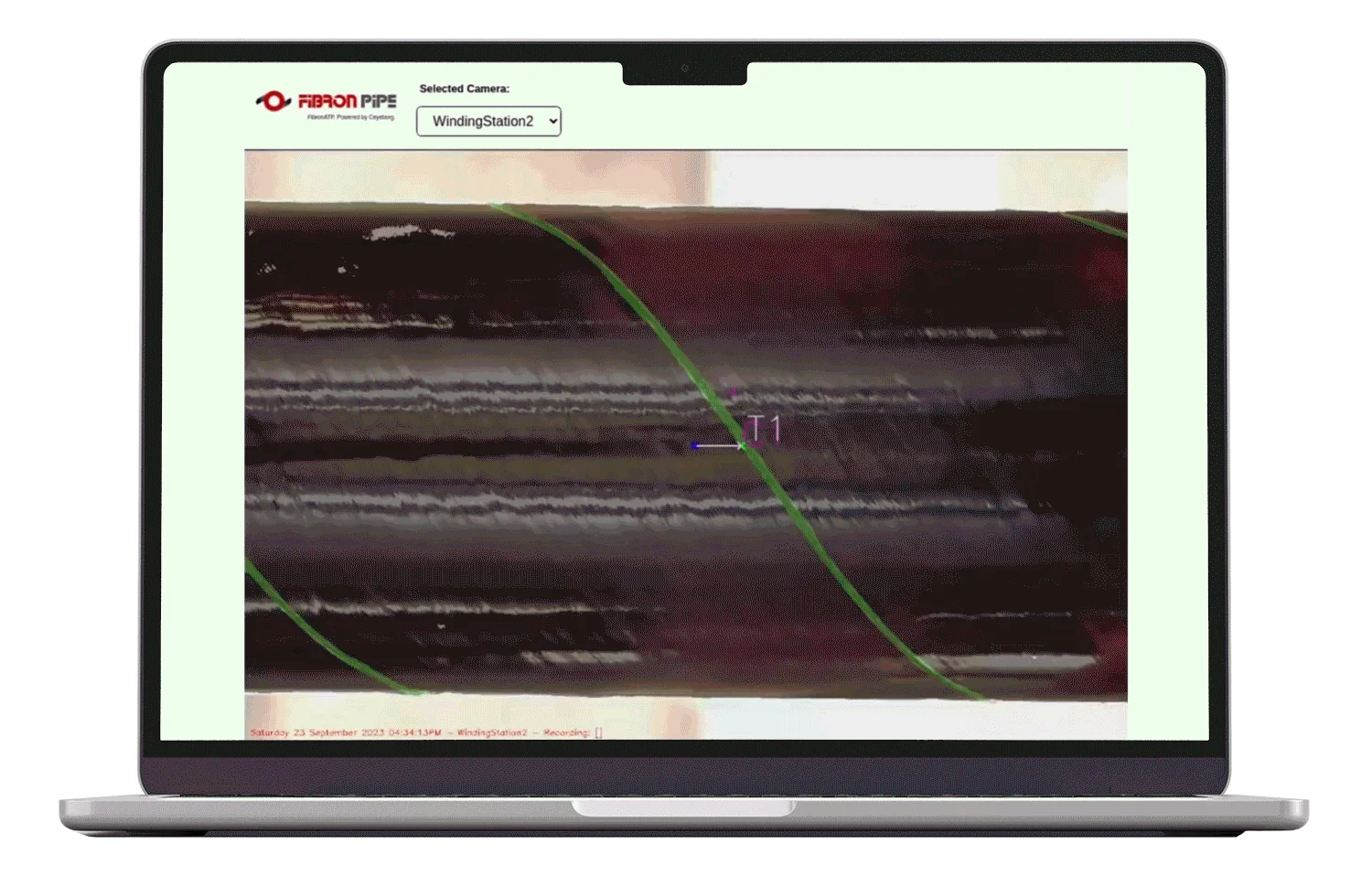
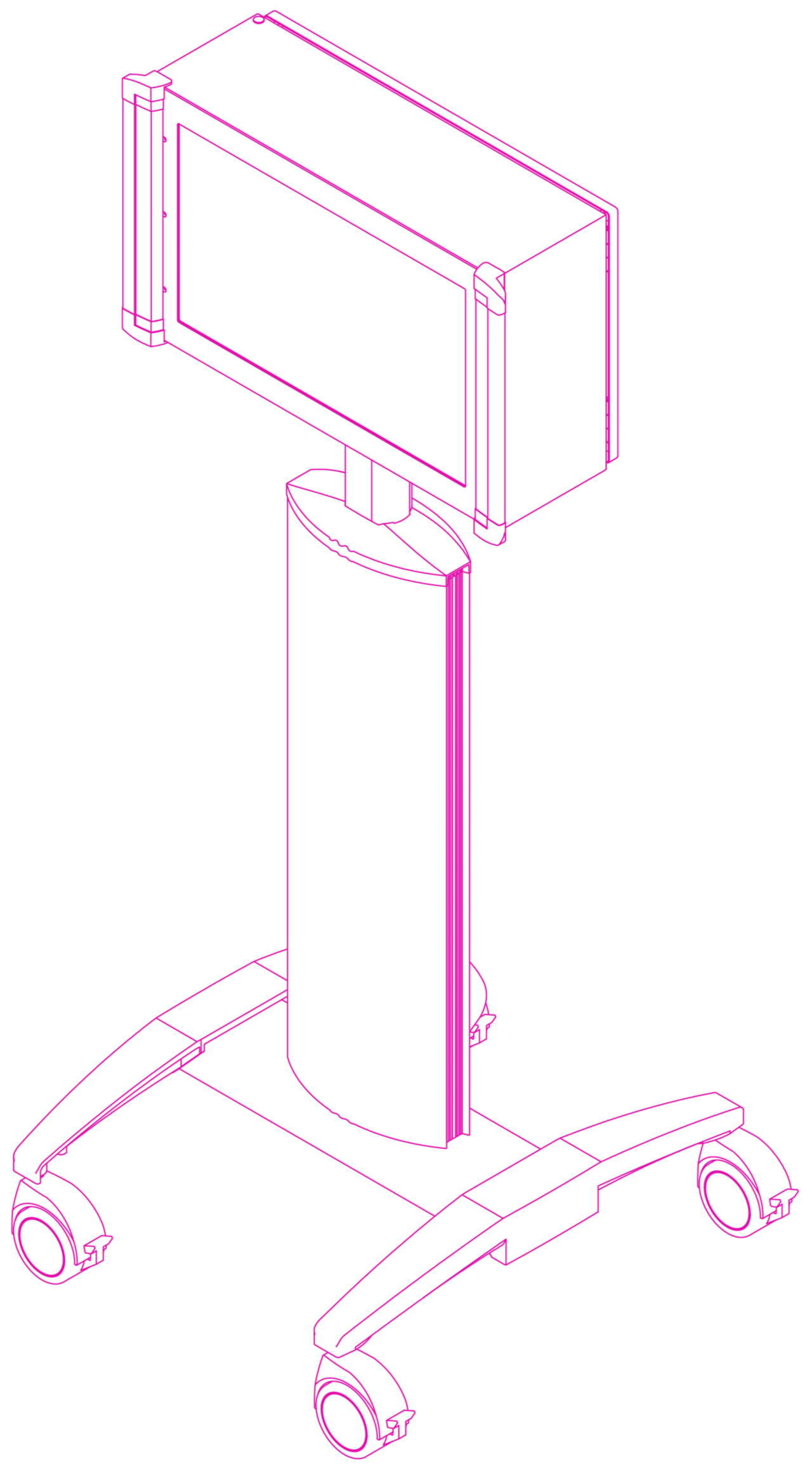
Custom-built Ceyeborg Terminal Station
Finally, the dimensions and classification of every gap or overlay produced was communicated back to the tape winder to control its tape placement head – guaranteeing an optimal placement and correctness throughout production, regardless of mechanical noise or other physical changes during production.
Ceyeborg constructed terminal stations for the operators to view the inspection system at any time. Our software’s web-based interface, allowed both on-site operators to quickly check the status of all stations, as well as remote personnel to securely view the pipe and the AI’s predictions during production, without being present at the factory line.
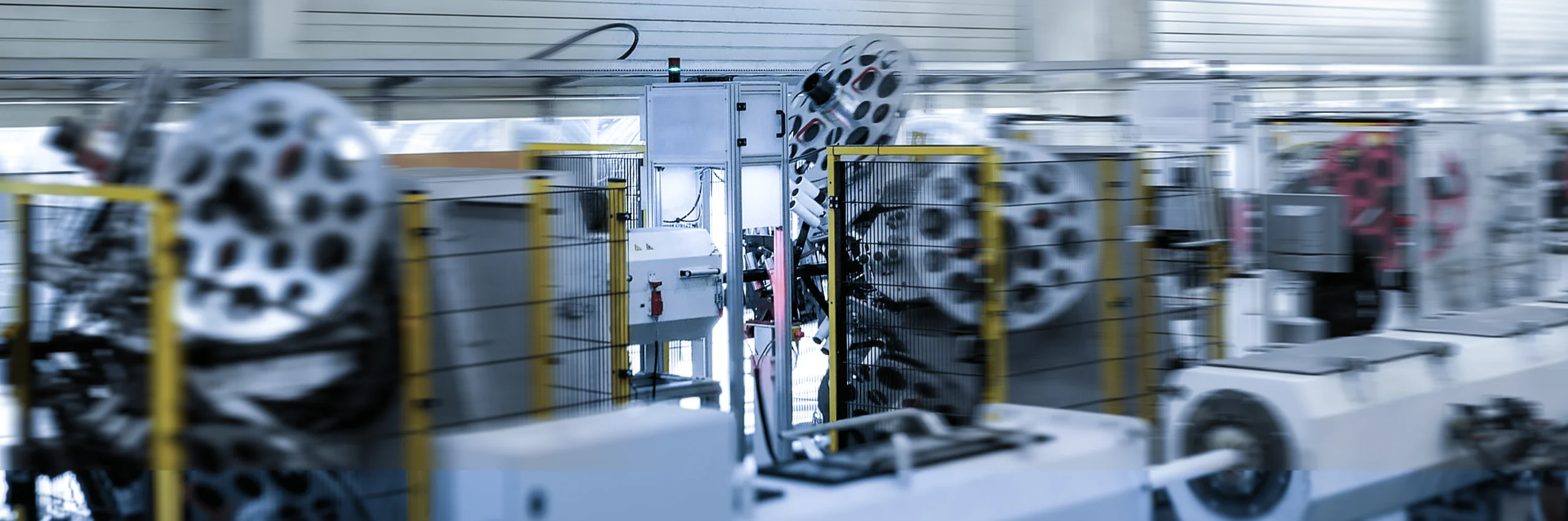
Result
Ceyeborg’s end-to-end AI-based inspection solution was successfully installed at FibronPipe’s facility and has automated the process of correcting the winders during production, which was done manually at all winding stations of the factory until this point. This freed up the line operators to perform other critical tasks during production and eliminated cases of tape placement “drift” during production. The integration of the AI-based inspection system into the FibronPipe’s programmable-logic control bus allows logging every event into a Ceyeborg-developed database. The detections of Ceyeborg’s AI-based inspection system together with the control decisions taken on the winding stations are used by FibronPipe to ensure the quality of every meter of pipe produced.
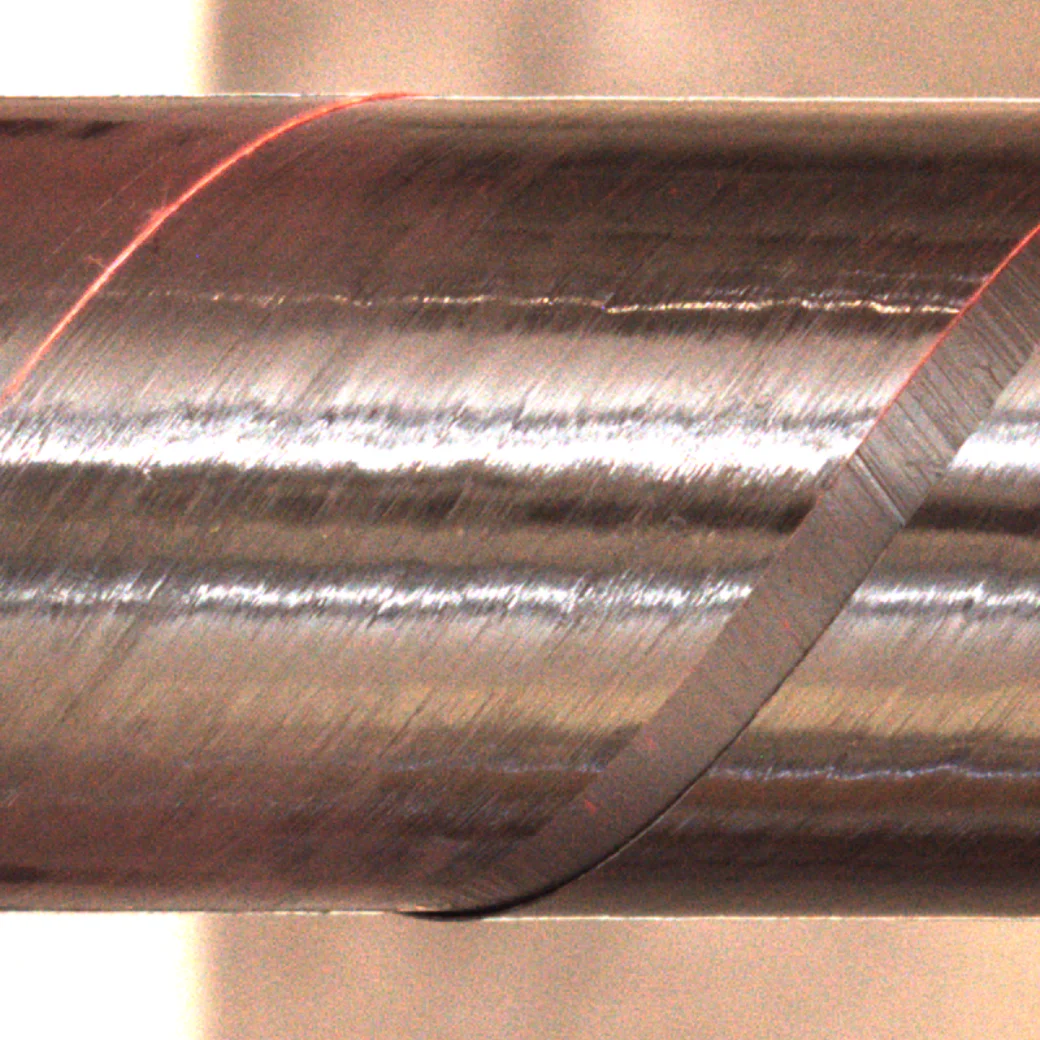
Without FibronATP:
Poor Placement, Large Gaps and
Overlays – Poor Bonding
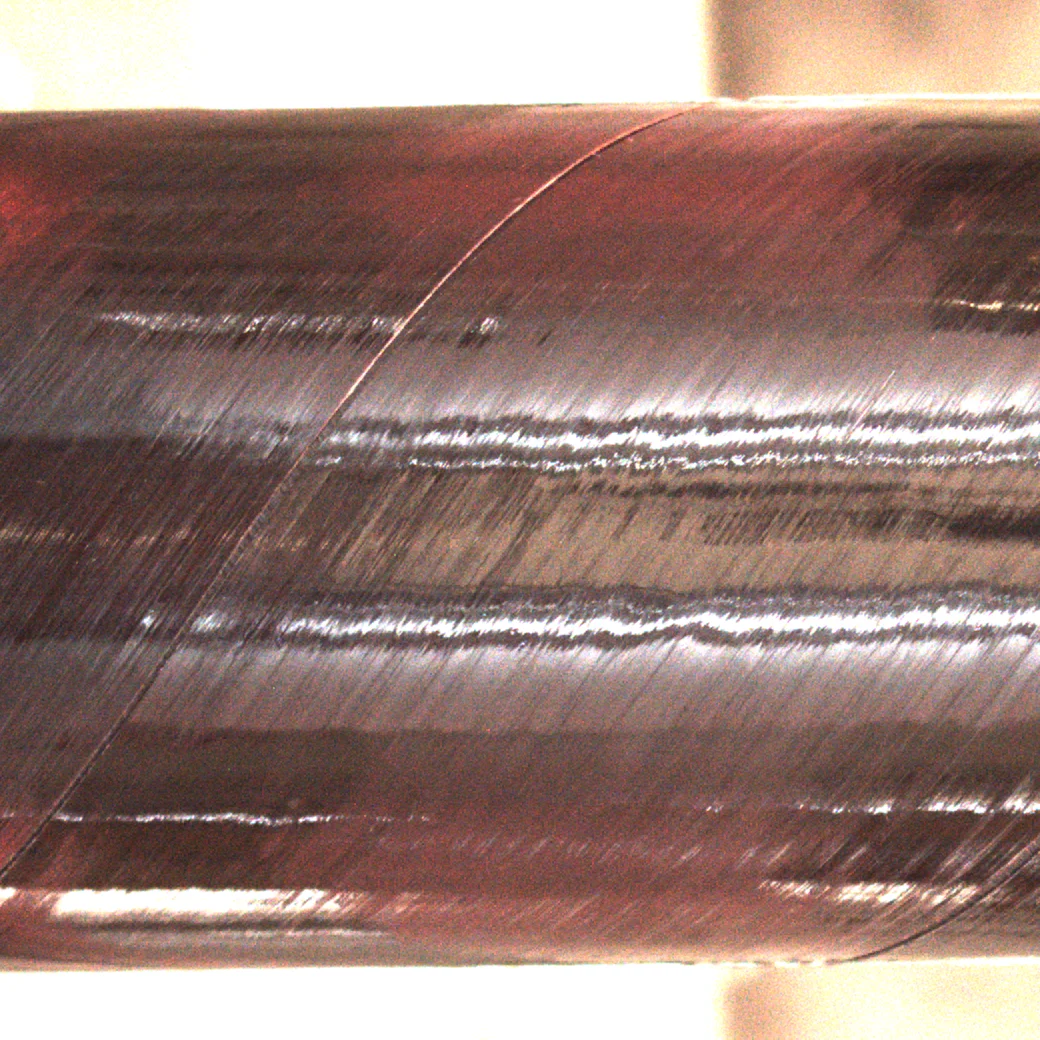
With FibronATP:
Optimal Automatic Tape Placement and
Optimal Gaps – Strong Bonding
Here are the resulting benefits after employing the ATP system:
- Speed and Efficiency:
AI-powered quality inspection systems are fast enough to analyse every inch of the production process of our customer. The tape placement process is monitored and controlled to maintain placement within optimal bounds, leading to seamless bonding of the tape during the heating process. Ceyeborg’s AI solution takes in mono-camera images and extracts the needed information using computer vision algorithms. This makes the monitoring process cost efficient in terms of hardware, and intelligent in terms of software. - Consistent Accuracy:
Different to human inspectors, AI systems do not experience fatigue or boredom, ensuring consistent inspections for extended periods of production. AI systems can learn from large datasets and identify the slightest deviations from quality standards. The consistency of AI inspection guarantees that every product is assessed with the same rigor, minimizing the risk of overlooking defects or inconsistencies that could impact the product’s quality. The AI records all its observations to an online database, which is shared with the customer as a digital certificate of quality for each purchase. - Continuous Learning:
The AI systems on FibronPipe’s factory lines are getting smarter every day. As the algorithms monitor the production of different pipe dimensions under different conditions, they “learn” to detect defects more accurately over time. This adaptability ensures that FibronPipe stays ahead of its competitors when it comes to emerging quality challenges and the identification of previously unknown defects. - Risk Minimization:
By employing a revolutionary quality inspection system, FibronPipe can reduce the risks for its customers. The AI systems can detect defects at an early stage and minimize the chances of product recalls and wasting materials. The long-term investment of FibronPipe in AI-powered quality inspection pays dividends to the customers, who will experience minimal downtime and maximum operational efficiency.