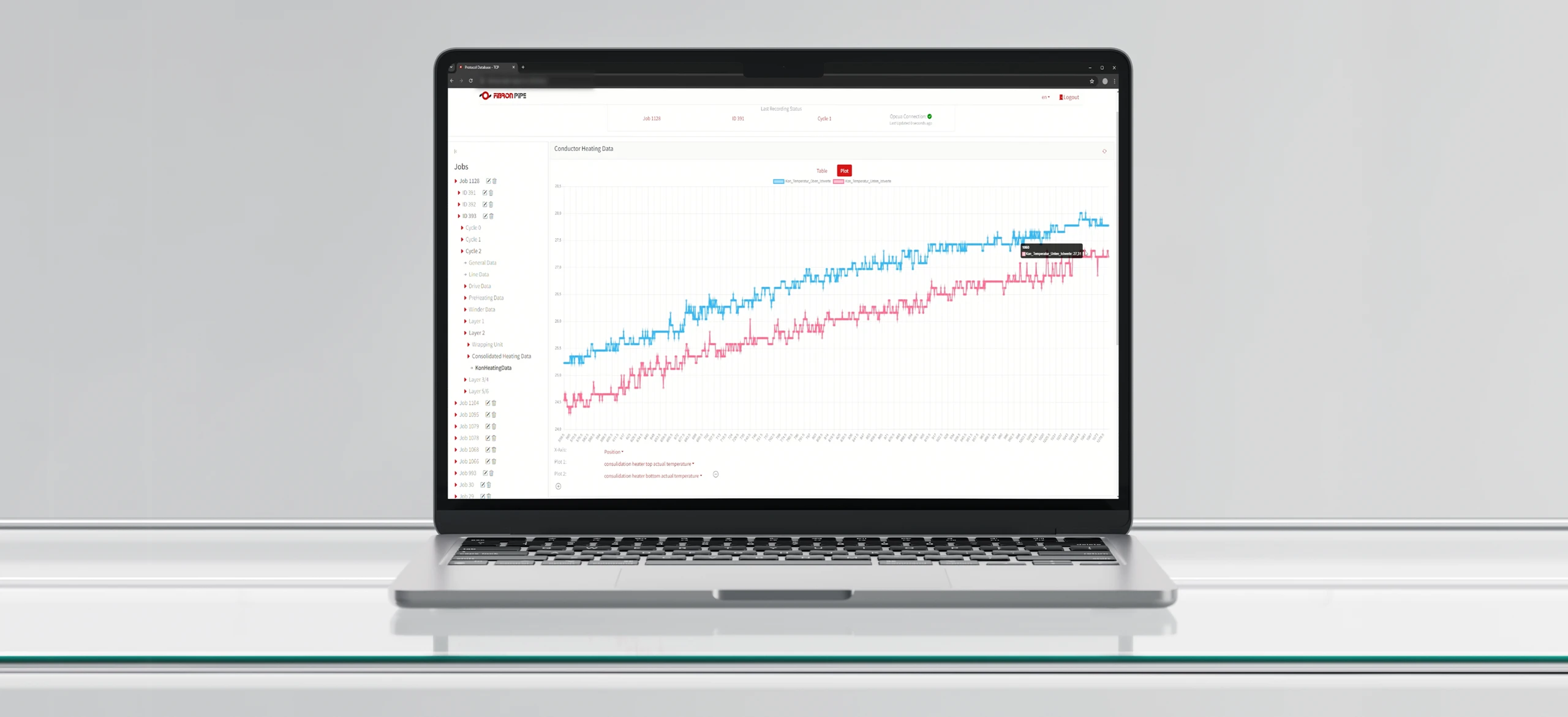
Inline Quality Assurance Database (Inline-QS)
A Symphony of Data and Quality Assurance
Challenge
FibronPipe GesmbH, a prominent manufacturer of thermoplastic composite pipes (TCPs), needed to track and correlate production statistics with the quality and longevity of their pipes. A key challenge was to monitor the multitude of sensors and actuators across the production line efficiently. The customer required a solution that would allow them to view real-time data from their entire production process at a glance and correlate this data with the quality metrics of each produced pipe. This need for comprehensive visibility and traceability was critical for maintaining high standards and identifying production inefficiencies swiftly through „Process Mining.“
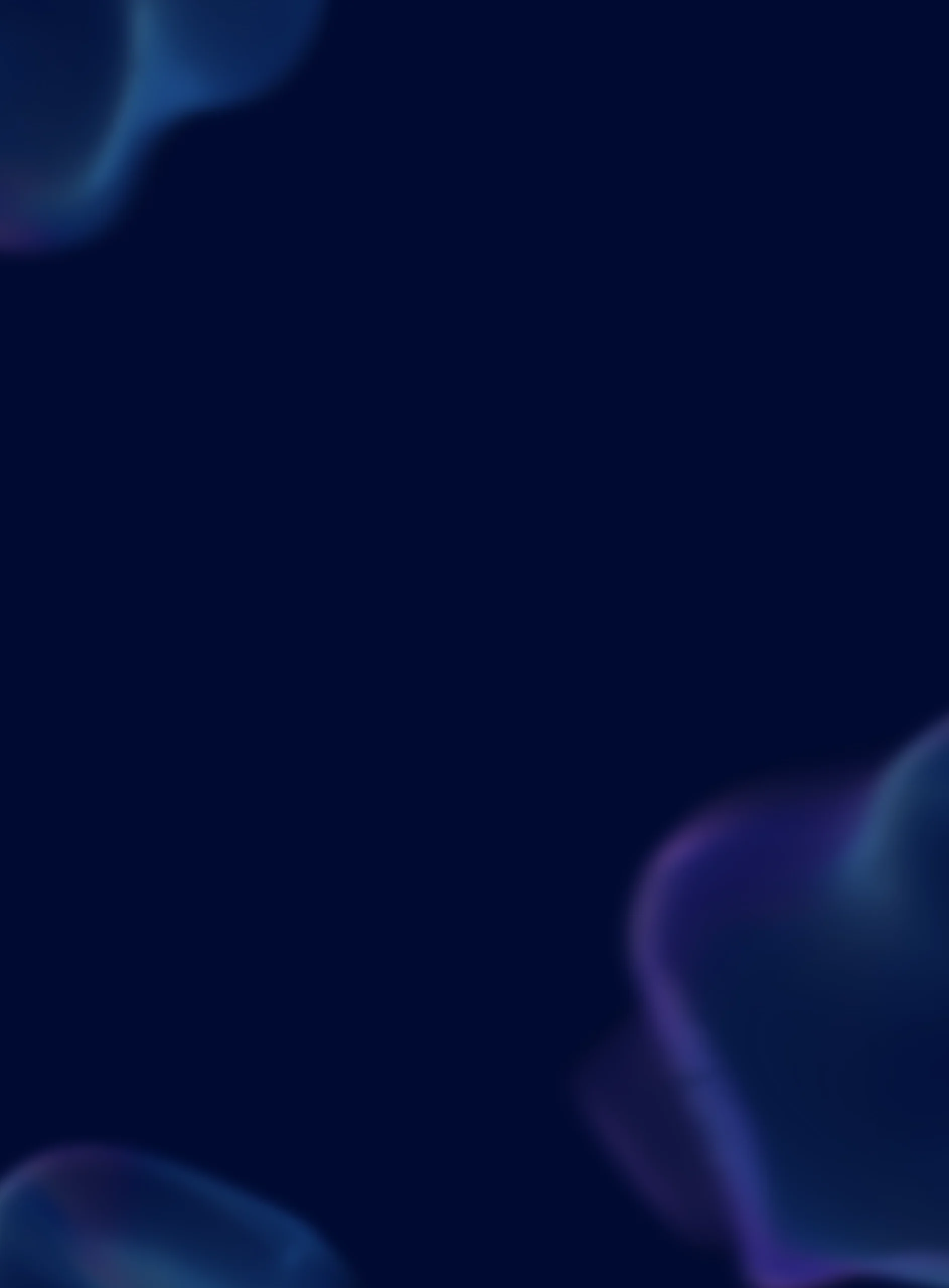
Solution
Ceyeborg devised a robust solution tailored to meet FibronPipe’s needs by implementing an advanced database system directly integrated into their production line. This Inline-QS (German: Inline-Qualitätssicherung, English: Inline Quality Assurance) framework captures all factory signals that form the product’s unique production history.
The system interfaced with the Programmable Logic Controller (PLC) using OPC UA (Open Platform Communications Unified Architecture), a standardized protocol for industrial automation. This setup enabled the continuous collection of data from all sensors and actuators involved in the production process.
The collected data was stored in scalable and reliable SQL-based databases. A custom-built, web-based user interface was developed, providing production engineers with real-time access to the data through the terminal station. Another benefit of the web-based application is enabling off-site staff to view production signals and production history at any time, anywhere, simply with an internet-enabled web browser. This interface featured advanced user management, allowing differentiated access levels to ensure secure data handling. The intuitive dashboard offered a comprehensive view of the entire production line, enabling engineers to monitor and correlate data effectively.
InlineQS interface for plotting production data at every meter of pipe production.
Additionally, the system allowed for detailed analysis of production anomalies and traceability of manufacturing faults, assisting in root cause analysis and continuous improvement efforts. This capability was crucial for maintaining quality standards and certifications such as API Standards.
To ensure all connected sensors and actuators of the production line were reachable at all times, Ceyeborg also certified the ethernet cables routed through the Automatic Tape Placement (ATP) stations to ensure InlineQS never misses any detail due to connection failures resulting from EMF noise of adjacent power cables or poor cable quality.
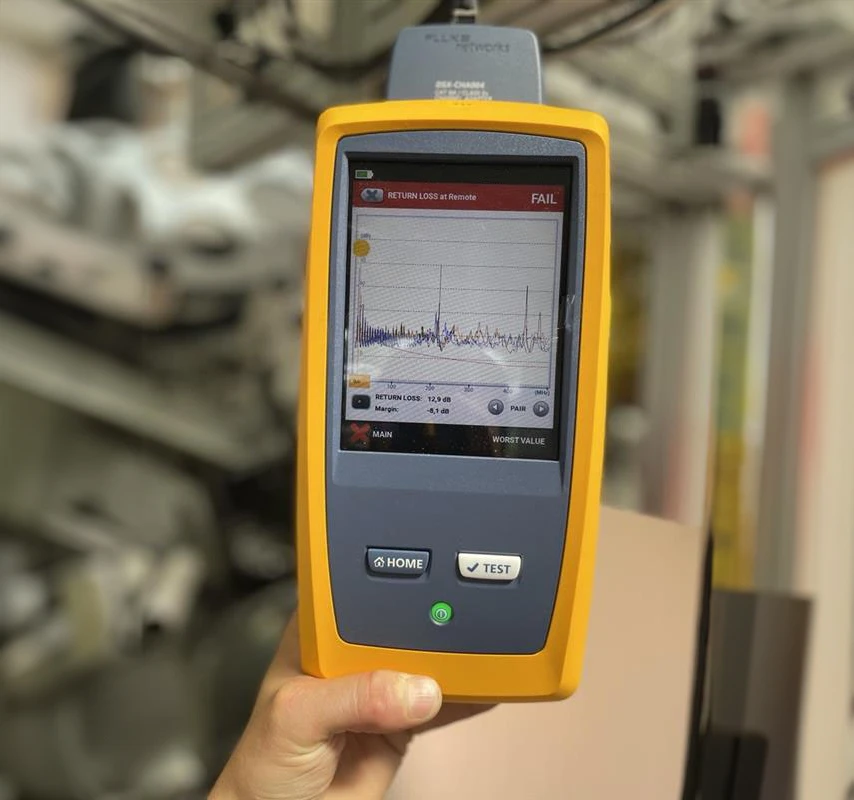
Cable certification for robust communication between factory equipment and InlineQS database
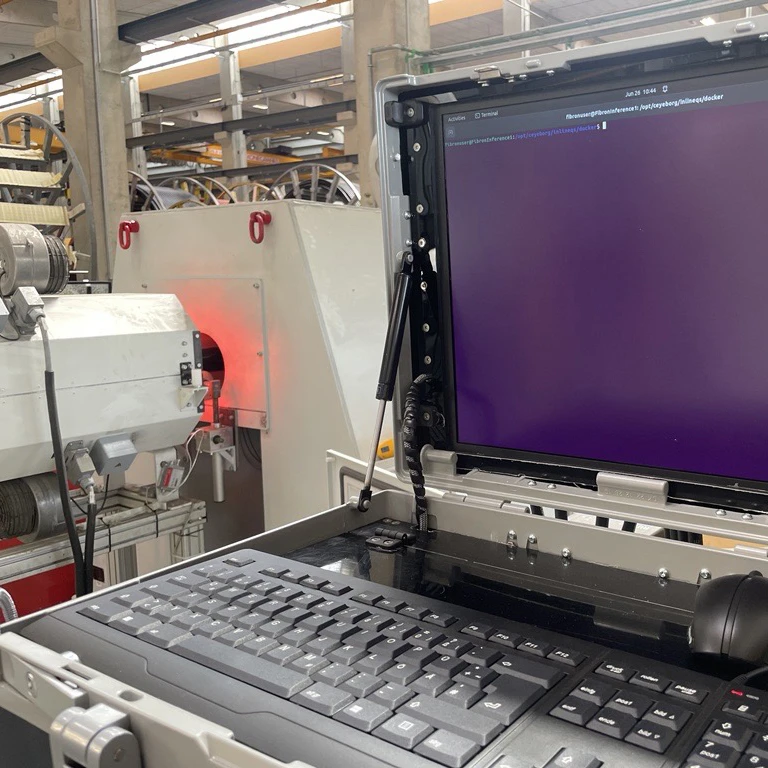
Custom-built Ceyeborg on-site debugging station
Result
The implementation of Ceyeborg’s solution transformed FibronPipe’s production monitoring capabilities. With the new database and interface, production engineers could now retrace every meter of pipe produced, correlating production conditions with the quality metrics of the final product. Over time, the extensive data collected allowed FibronPipe to refine their production process further. By analyzing historical data, they optimized the settings for sensors and actuators, improving overall production efficiency and reducing waste. The real-time monitoring and alerting features minimized downtime and enhanced decision-making speed, significantly boosting operational effectiveness.
Here are the concrete benefits gained by our customer:
- Trust in Data:
Recording and preserving the unique production history of every pipe offers end-users of the product the ultimate trust in the manufacturing process of their assets. Every step of the process, from sourcing the materials to production and testing can be stored and accessed by the customer in a secure online database. The customer can see the production details per meter at each layer of the purchased pipe’s internal construction. The AI-based quality inspection metrics are also logged to the same database. The recorded production history proves that the product has undergone meticulous checks and adherence to the highest standards. This digital certificate is a commitment to quality which customers can check for themselves and have peace of mind in their purchase. - Process Mining and Data Analysis:
Over time as more pipes are deployed, the Inline-QS recorded data grows into Big Data which can be analysed for process mining. Our customer can analyse the performance of the product in different applications, regions, and environmental conditions, enabling the research and development of improved pipes customized for different applications. Data-driven optimization can help pinpoint areas of improvement to enhance productivity, reduce waste and mitigate errors. The path towards future excellence becomes clearer and more attainable over time. - Compliance and Certification:
Inline-QS professional online databases enable fast traceability and transparency of all relevant production details. This facilitates the process of auditing the manufacturing standards and certification of the product. Inline-QS protects both FibronPipe and its end-customers from deviations in quality standards. - Competitive Advantage:
A product sold with a digital certificate containing every production detail recorded is a powerful differentiator in the industry. Customers are rightfully demanding higher standards and better guarantees of safety and reliability. By offering direct access to the production details of every purchased pipe, FibronPipe maintains it position as a leader in transparency, quality control, and continuous improvement.